Upper floor structures serve a dual purpose: not only do they provide an additional living space above a lower level, but they also accommodate essential services such as plumbing, electrical wiring, heating pipes, ventilation, and even central vacuum system pipework. This guide will delve into the cost considerations that accompany the construction of upper floors in your Irish home. From material selection to sound insulation, we’ll break down the factors that play a role in determining the expense, all while ensuring that the information remains accessible to everyone.
Material Matters: Key Considerations for Upper Floors
The Role of Material Selection
When it comes to the cost of an upper floor, whether it’s the first floor or an attic floor, the primary factor influencing the expense is the choice of materials used in the structure. Each material option comes with its set of advantages and drawbacks, influencing various aspects of the floor’s performance and cost.
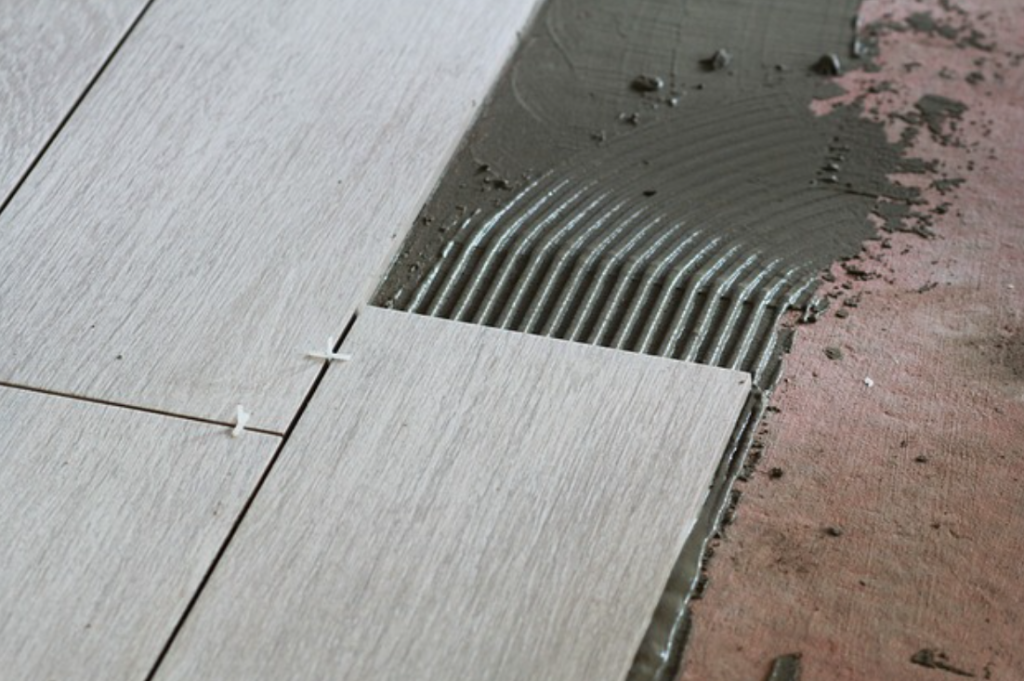
Engineer’s Expertise: Designing for Stability and Compliance
Before delving into specific material options, it’s important to highlight the role of a qualified engineer in the process. An engineer will assess the loadings specific to your structure and design the supports’ size, depth, and makeup to align with the building’s layout, floor spans, and compliance with Building Regulations. This professional oversight ensures a structurally sound and safe upper floor.
Traditional Cut Timber Floors: A Familiar Choice
In the past, timber dominated the construction of floor structures. Kiln-dried softwood joists were commonly used to span between structural walls. A carpenter would install these joists after the completion of the blockwork lift from the ground to the first floor. Internal load-bearing walls provided support for the timber on mid spans, with additional joists added for reinforcement.
While this setup facilitated the passage of services, its susceptibility to shrinkage over time resulted in squeaky floors—a common issue that many homeowners experienced. Sound transfer, especially the impact of walking, posed another challenge. Various solutions, including rubber membranes and underlays, attempted to address this issue.
Timber I-Joists: A Modern Approach
A contemporary alternative to traditional joists involves the use of timber I-joists, often referred to as I-beams. These factory-made joists feature an I-shaped cross-section, combining softwood or laminated veneered timber with an engineered board center web. They offer durability, lightweight construction, and the ability to span over 6 meters without internal support. The avoidance of shrinkage-related problems adds to their appeal. However, sound impact issues remain similar to those of traditional joists.
Metal Web Joists: Strength and Simplicity
Metal web joists share a visual resemblance with I-joists but incorporate a wavy metal web center for services without the need for drilling. These joists are strong, easy to carry, and installation-friendly. They can achieve unsupported spans of up to 7.5 meters and offer resistance to shrinkage-related problems. The challenges related to sound impact persist, though.
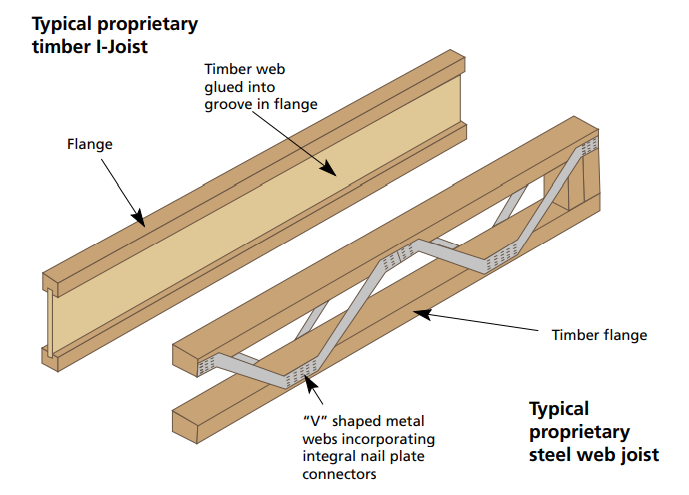
Timber Frame Construction: A Holistic Approach
Timber frame companies often provide complete systems for upper floors, frequently using one of the mentioned joist systems. Ensuring clarity on the specified system in each quotation is crucial for accurate cost assessment.
Hollowcore Precast Concrete: Speed and Strength
The popularity of precast concrete floors has surged due to their efficient factory manufacturing and swift on-site installation. Precast hollow core flooring, the most common type, features concrete slabs with voids that reduce weight. These slabs come in varying thicknesses and spans, providing excellent sound insulation and fire resistance.
However, routing services within the voids and potential coring costs must be considered. Despite these challenges, precast concrete floors excel in reducing sound transfer. They also accommodate underfloor heating systems, making them versatile in achieving desired comfort levels.
Comparing Costs: A Practical Overview
For a better understanding of costs, let’s examine a notional property with a 67.5 square meter first-floor area. This analysis encompasses standard 12.5mm plasterboard ceilings below and tiled floor finishes above, along with an allowance for floor tile purchase. The table below offers an overview of costs, excluding openings and accessories.
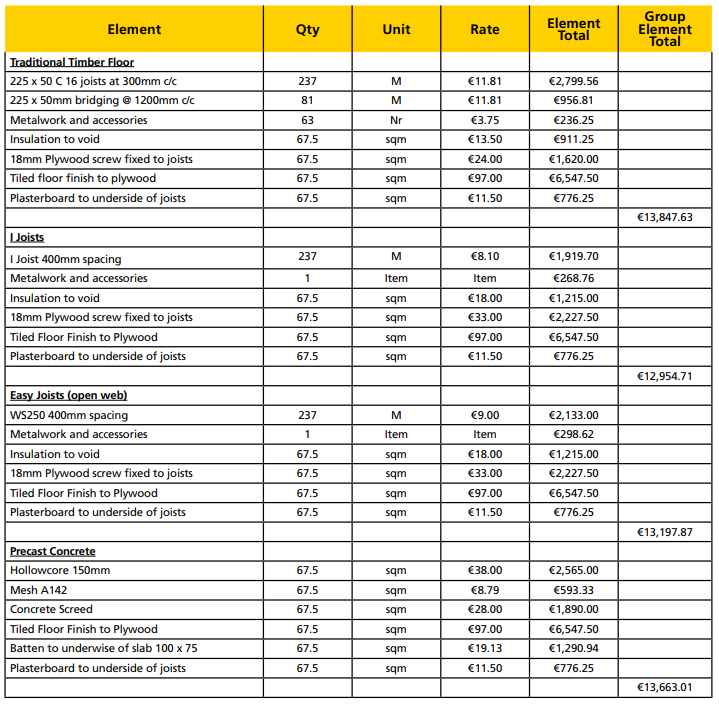
In Conclusion: Understanding Your Floor Options
When it comes to estimating the cost of upper floors in your Irish home, various factors come into play, from material choices to structural design. While each option presents its own set of advantages and challenges, the goal is to strike a balance between budget considerations and long-term comfort and durability. By understanding the characteristics of different materials and seeking professional guidance, you can make informed decisions that align with your needs and aspirations. With this guide as your starting point, you’ll be well-equipped to embark on your upper floor construction journey with confidence and clarity.